The production steps involved in
positioning sheet cutting machines can vary depending on the specific machine model and manufacturer. However, here is a general outline of the typical production steps for positioning sheet cutting machines:
Design and Planning: The first step is to design and plan the positioning sheet cutting machine. This involves determining the required specifications, such as the maximum sheet size, cutting accuracy, cutting speed, and any additional features or functionalities.
Procurement of Components: Once the design is finalized, the necessary components and materials are procured. This may include mechanical parts, electrical components, motors, sensors, control systems, and cutting tools.
Assembly of Mechanical Structure: The mechanical structure of the positioning sheet cutting machine is assembled according to the design specifications. This involves constructing the frame, installing guide rails, mounting cutting blades or tools, and integrating any additional mechanisms required for precise positioning and cutting.
Installation of Electrical and Control Systems: The electrical and control systems are installed on the machine. This includes wiring, connecting motors and sensors, and integrating the control panel or HMI (Human-Machine Interface) for operating the machine.
Calibration and Testing: Once the mechanical and electrical components are in place, the machine undergoes calibration and testing. This ensures that all axes and movements are accurately aligned and calibrated for precise sheet positioning and cutting. It also involves testing the functionality of control systems, sensors, and safety features.
Integration of Software and Programming: The positioning sheet cutting machine is programmed with the necessary software to control its operation. This includes creating cutting patterns, setting cutting parameters, and implementing any automation or customization required for specific applications.
Quality Control and Inspection: Before the machine is released for production or sale, it undergoes rigorous quality control and inspection processes. This includes checking the accuracy of cutting, ensuring the machine operates smoothly and reliably, and verifying compliance with safety standards.
Packaging and Shipping: Once the positioning sheet cutting machine passes quality control, it is prepared for packaging and shipping. It is carefully packed to prevent damage during transportation and shipped to the designated destination.
It's important to note that the production steps may vary based on the complexity of the positioning sheet cutting machine and the manufacturer's specific processes. Advanced machines may include additional steps such as laser alignment, automated material handling systems, or integration with computer-aided design (CAD) software for enhanced precision and efficiency.
It's recommended to consult the manufacturer's documentation or reach out to them directly for detailed information on the production steps specific to their positioning sheet cutting machines.Meanwhile,The structure of positioning sheet cutting machines can vary depending on the specific model and manufacturer. However, here is a general overview of the typical structure of positioning sheet cutting machines:
Frame: The frame forms the base structure of the machine and provides stability and support. It is usually made of rigid materials such as steel or aluminum to withstand the cutting forces and maintain accuracy during operation.
Cutting Head: The cutting head is the main component responsible for cutting the sheet material. It typically consists of a cutting tool or blade, which can be a rotating blade, oscillating blade, laser, water jet, or other cutting mechanisms depending on the specific machine type. The cutting head is mounted on a carriage or gantry system that allows precise movement along the X, Y, and sometimes Z axes.
Sheet Positioning System: Positioning sheet cutting machines are designed to accurately position the sheet material for cutting. This system typically includes one or more clamps, grippers, or vacuum suction devices to hold the sheet securely in place during the cutting process. It may also incorporate sensors or vision systems to detect the edges or alignment of the sheet material and ensure accurate positioning.
Drive Systems: Positioning sheet cutting machines utilize various drive systems to control the movement of the cutting head and the sheet material. These drive systems can include stepper motors, servo motors, linear actuators, or hydraulic/pneumatic systems, depending on the machine design. The drive systems are connected to the control system and enable precise and synchronized movements of the cutting head and sheet material.
Control System: The control system is the brain of the positioning sheet cutting machine. It includes a control panel or human-machine interface (HMI) that allows operators to input cutting parameters, control the machine's movements, and monitor its operation. The control system may also include programmable logic controllers (PLCs), software, and communication interfaces for data exchange and integration with other systems.
Safety Features: Positioning sheet cutting machines are equipped with safety features to protect operators and prevent accidents. These features can include emergency stop buttons, safety interlocks, protective barriers, and sensors to detect obstructions or abnormal conditions during operation.
Optional Accessories: Depending on the specific machine and application, positioning sheet cutting machines may have additional accessories or features. These can include material feeding systems, waste extraction systems, material alignment guides, automatic tool changers, or dust collection systems to enhance productivity and efficiency.
It's important to note that the structure and components of positioning sheet cutting machines can vary significantly depending on the machine type, size, and manufacturer. It's recommended to consult the machine's documentation or reach out to the manufacturer for detailed information on the specific structure and features of their positioning sheet cutting machines.
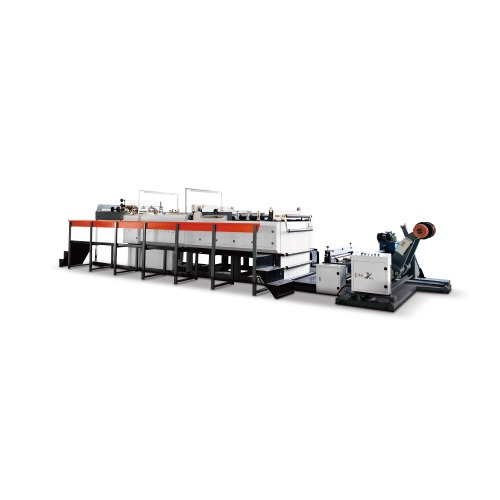