Laminating Capacity: Determine the maximum size and thickness of cardboard that the laminating machine can handle. Consider the dimensions and weight of the cardboard sheets you plan to laminate to ensure they fit within the machine's specifications.
Laminating Speed: Evaluate the laminating speed of the machine, which is usually measured in feet per minute (FPM) or meters per minute (MPM). Choose a machine that offers a laminating speed that aligns with your production requirements.
Heating Method: Cardboard laminating machines use different heating methods, such as hot rollers or thermal oil. Hot roller machines are commonly used for laminating cardboard, providing even heat distribution and consistent lamination results. Thermal oil-based machines may offer faster heating and cooling times.
Temperature Control: Look for a laminating machine that offers precise temperature control. This is important to ensure proper lamination without damaging the cardboard or the laminating film. Machines with digital temperature control and adjustable settings provide more flexibility.
Film Compatibility: Consider the types of laminating films that the machine is compatible with. Common films used for cardboard lamination include polypropylene (PP), polyester (PET), or thermal laminating films. Ensure that the machine can accommodate the specific film type and thickness you intend to use.
Ease of Use: Look for a machine that is user-friendly and easy to operate. Features such as intuitive controls, clear instructions, and a straightforward loading system can enhance the user experience and reduce the learning curve.
Durability and Build Quality: Assess the overall durability and build quality of the laminating machine. It should be constructed from robust materials to withstand continuous use and provide long-lasting performance. Look for machines from reputable manufacturers known for producing reliable equipment.
Maintenance and Servicing: Consider the maintenance requirements of the machine. Look for machines that are easy to clean and maintain, with accessible parts and clear maintenance instructions. Additionally, check if the manufacturer provides reliable after-sales service, including technical support and access to spare parts.
Safety Features: Ensure that the laminating machine incorporates necessary safety features, such as emergency stop buttons, safety sensors, and heat shields. These features help prevent accidents and protect the operator from potential hazards.
Cost and Budget: Consider your budget and the overall cost-effectiveness of the machine. Compare prices and features of different models to find a machine that offers a good balance between cost and performance.
By considering these factors, you can choose a cardboard laminating machine that suits your specific needs, whether it's for small-scale or industrial-level production. It's recommended to consult with manufacturers or suppliers, review product specifications, and potentially request demonstrations or samples to assess the suitability of the machine for your requirements.Besides,The working principle of cardboard laminating machines involves the application of heat and pressure to bond a layer of laminating film onto a cardboard surface. The specific steps and mechanisms may vary depending on the type and model of the machine, but the general working principle is as follows:
Preparation: Before starting the laminating process, ensure that the cardboard sheets and laminating film are properly prepared and cut to the desired sizes.
Heating: The laminating machine typically features heating elements, such as heated rollers or plates. These elements are responsible for providing the necessary heat to activate the adhesive layer on the laminating film. The machine is preheated to the appropriate temperature required for the specific type of laminating film being used.
Feeding: Place the cardboard sheet to be laminated onto the feeding tray or rollers of the laminating machine. Ensure proper alignment and positioning of the sheet to prevent misalignment during the laminating process.
Film Application: The laminating film is fed into the machine, either from a roll or pre-cut sheets. The film passes through the heated rollers or plates, where the heat activates the adhesive layer on the film.
Pressure Application: Once the laminating film is heated, it comes into contact with the cardboard sheet. The machine applies pressure, typically through pressure rollers or plates, to firmly press the laminating film onto the cardboard surface. The pressure ensures proper adhesion and eliminates air bubbles or wrinkles between the film and the cardboard.
Cooling and Finishing: After the laminating film is bonded to the cardboard, the laminated sheet passes through cooling rollers or a cooling system to allow the adhesive to set and solidify. This step helps in achieving a smooth and flat laminated surface.
Trimming and Cutting (Optional): Depending on the desired outcome, the laminated cardboard sheets may undergo additional trimming or cutting to remove any excess film or achieve specific dimensions or shapes.
Output: The laminated cardboard sheets are discharged from the laminating machine, ready for further processing, packaging, or use.
Throughout the laminating process, it's important to maintain proper temperature, pressure, and feeding speed to ensure consistent and high-quality lamination results. Additionally, some advanced laminating machines may include features such as adjustable temperature control, variable speed settings, or multiple heating and cooling zones to provide greater control and versatility.
It's crucial to follow the manufacturer's instructions and guidelines specific to the laminating machine being used to ensure safe and efficient operation.
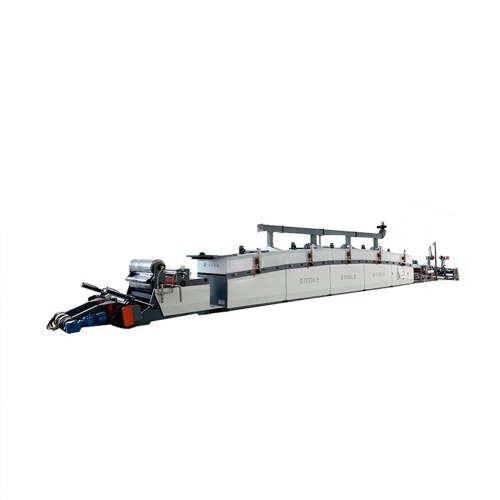