The foil stamping embossing machine may encounter the following common problems during operation:
Poor foil stamping effect: Issues such as uneven foiling, insufficient color saturation, or blurry foiling patterns may occur during the foiling process. This could be due to improper settings of foiling temperature, pressure, or time.
Inconsistent embossing depth: Inconsistent embossing effects, with some areas deeply embossed while others lightly embossed, may result from worn embossing wheels, uneven pressure distribution, or differences in material thickness.
Material damage: Problems such as tearing, wrinkling, or deformation of materials during foiling or embossing may result from excessive pressure, high temperature, or material incompatibility.
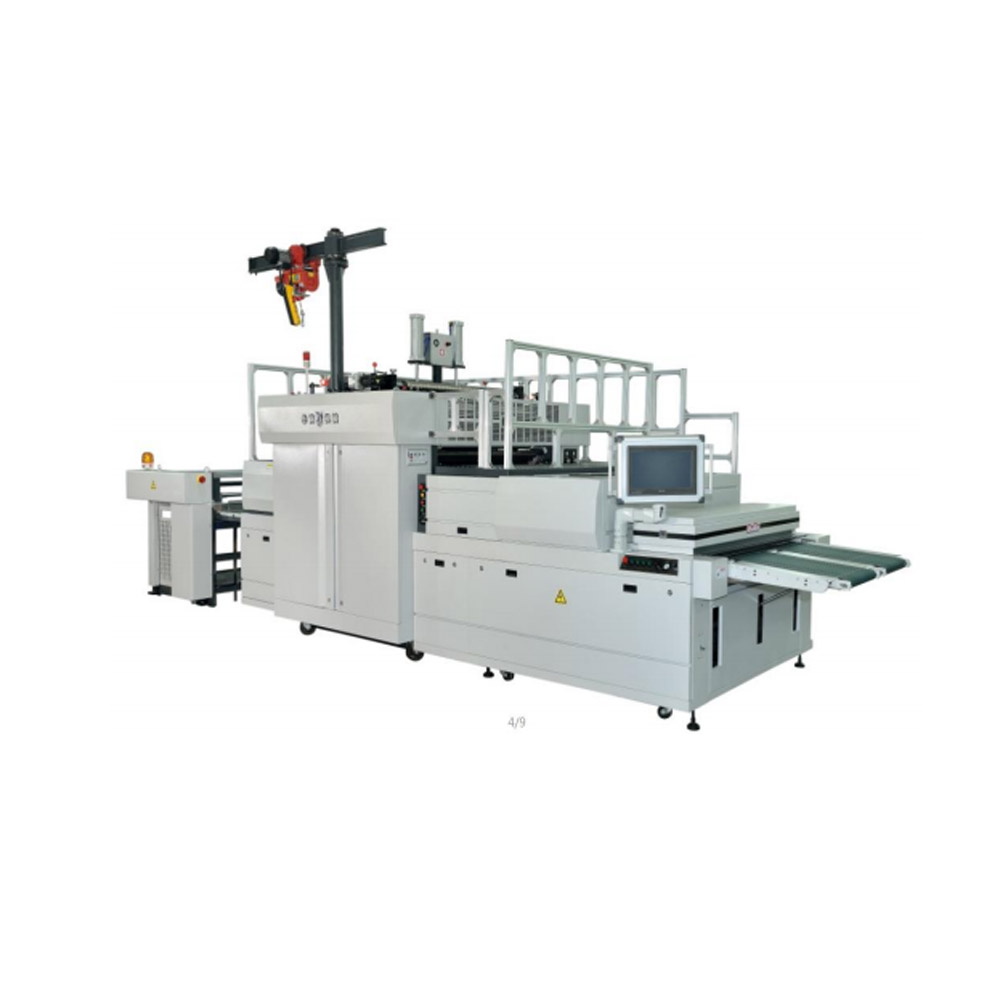
Electrical faults: Electrical issues such as startup failure, malfunctioning display screens, or unresponsive buttons may be related to components such as power connections, switches, driver boards, or main control boards.
Mechanical malfunctions: After prolonged use, the foil stamping embossing machine may experience mechanical faults such as conveyor belt misalignment, roller jamming, or wear and tear of guide rails, affecting operational continuity and stability.
Ink blockages: The ink system of the
foil stamping machine may experience blockages, leading to the inability to supply ink properly and affecting the foiling effect.
Unstable temperature control: Instability in temperature control during foiling may result in color variations or inconsistencies in foiling.
These problems may occur individually or be interconnected, impacting the normal operation of the foil stamping embossing machine and the quality of the final products. To avoid and address these issues, operators need to regularly inspect the equipment, pay attention to material selection and compatibility, and adjust process parameters reasonably. Additionally, for electrical and mechanical faults, professional maintenance personnel should be contacted promptly for inspection and maintenance.